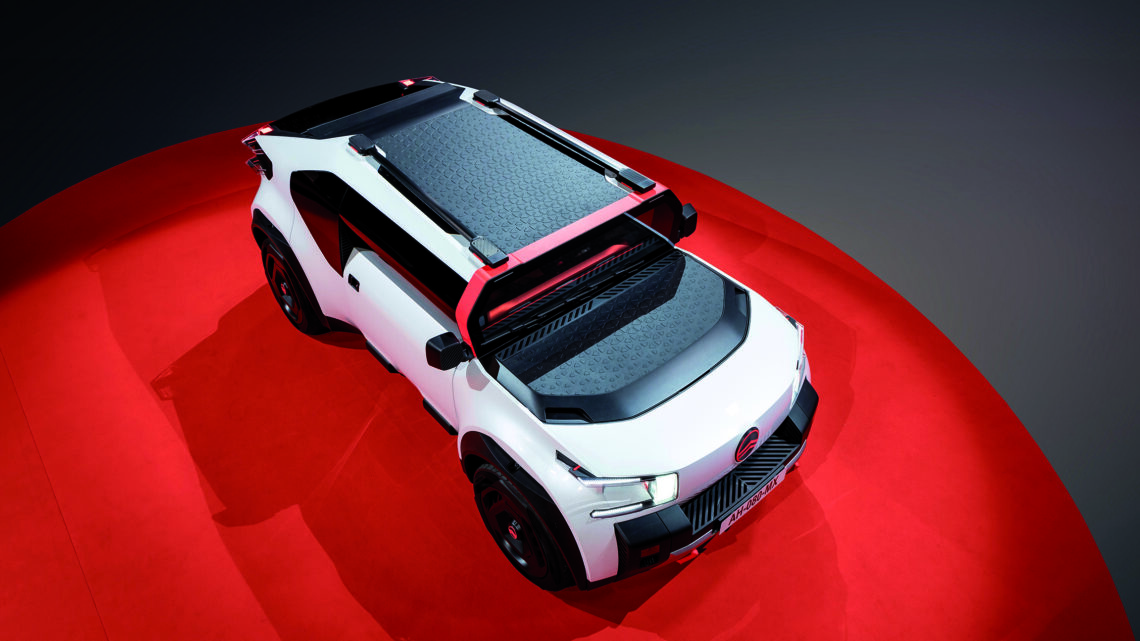
LEGGEREZZA ALLA GUIDA
Gennaio 23, 2023Elettrica o no, l’auto è smart: rimodellata in peso, design, emissioni di CO2, processi produttivi
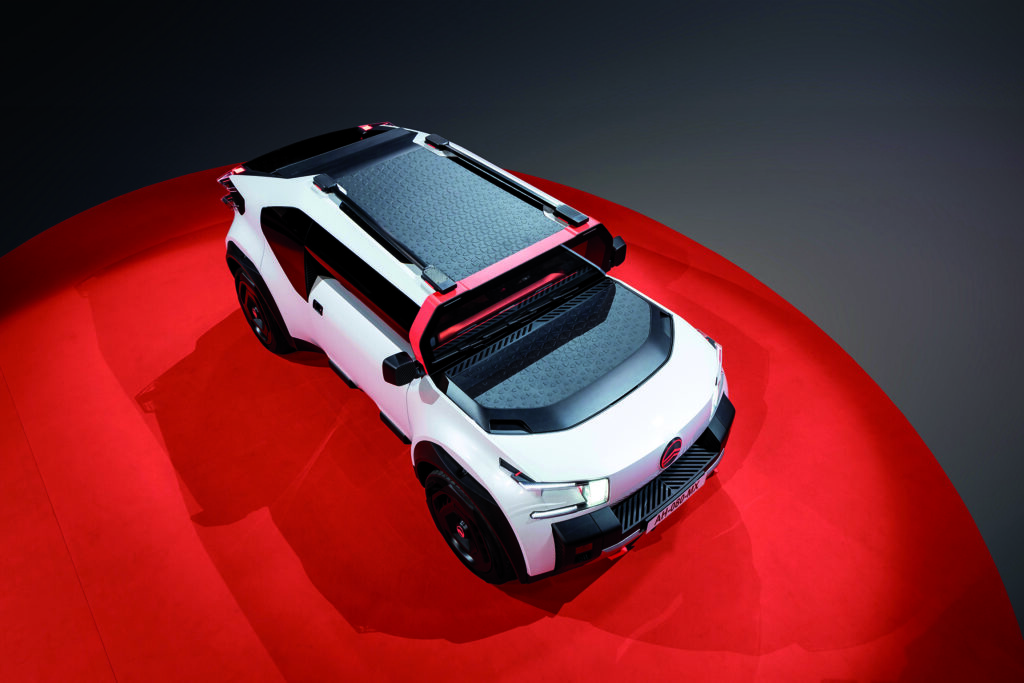
L’e-mobility è alle porte, ma non sostituirà rapidamente né completamente il panorama delle quattro ruote. La riorganizzazione che essa implica è davvero ingente nei costi, nella creazione di infrastrutture e anche nella mentalità di molti consumatori: vissuta come status symbol di ricchezza e potere, un’auto attaccata alla presa richiama ancora a molti un prosaico elettrodomestico.
I temi della leggerezza, della sostenibilità e di un design più libero e hi-tech sono tuttavia vincenti su tutte le gamme e le motorizzazioni, promossi al meglio da polimeri e materiali compositi.
MECCANICHE DEL DESIDERIO
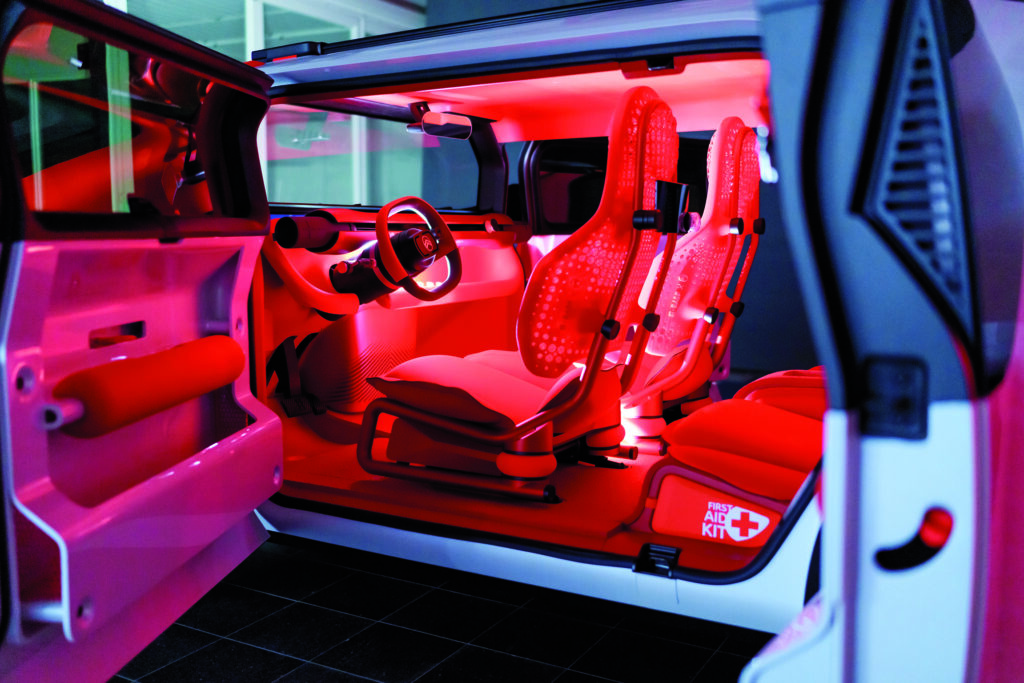
Oli è la contrazione di all ë: un’auto ‘manifesto’ che Citroën e Basf hanno sviluppato insieme per dimostrare “come ridurre al minimo l’impatto ambientale riportando il piacere della guida a un veicolo elettrico e funzionale”, spiega Laurence Hansen, Product & Strategy Director presso la Casa automobilistica. Un modello è la 2CV, di cui la colorata concept Oli replica l’accelerazione, limitando la velocità di crociera a 110 km/h per incrementare l’autonomia e la durata della batteria. Nell’adozione di materiali contemporanei molti componenti sono soggetti a un ripensamento radicale: per esempio, gli schienali dei sedili sono realizzati con 3D printing da Sculpteo, service di Basf, usando il TPU88A Ultrasint in una struttura lattice che garantisce traspirabilità eliminando la necessità di sistemi di ventilazione. Per ridurre il fabbisogno di stampi e attrezzature le portiere del conducente e del passeggero sono identiche, e così i passaruota e i paraurti; inoltre, per favorire il riciclo meccanico del veicolo a fine vita, diverse parti utilizzano materiali appartenenti alla stessa famiglia di polimeri. Il TPU espanso Infinergy è usato per i braccioli e il pavimento vettura: elastico come la gomma, è leggero, robusto, resistente alle abrasioni, ammortizza rumori e abrasioni, è waterproof e, grazie al rivestimento a base acqua NovaCoat-P, è protetto da UV, sporco e agenti chimici, idoneo ad accogliere le prese, prodotte con un altro poliuretano termoplastico di Basf, Elastollan. Il cofano, il tetto e il bagagliaio sono costituiti da pannelli che abbinano il sistema poliuretanico Elastoflex e la verniciatura spray Elastocoat: la struttura sandwich a nido d’ape riduce il peso conservando elevata stabilità.
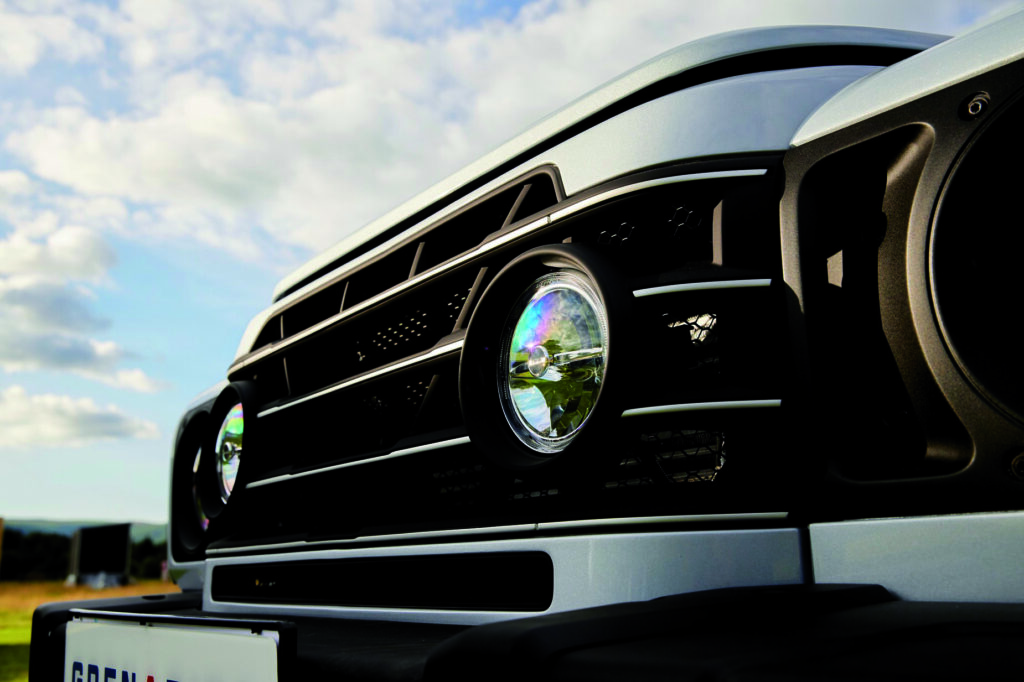
D’altro segno la genesi della 4×4 Ineos Grenadier, desiderata da Jim Ratcliffe, il proprietario di Ineos Styrolution, per ricreare in una nuova vettura la Land Rover Defender, la cui produzione è stata interrotta nel 2016. La prima produzione di Ineos Automotive è supportata da Magna Styr nello sviluppo dell’engineering e monta una propulsione di BMW; i prossimi modelli a zero emissioni adotteranno la tecnologia fuel-cell di Hyundai. Per la griglia frontale, caratterizzata da stabilità dimensionale, resistenza all’impatto, superficie inalterabile agli UV, al calore e agli agenti atmosferici, è stata scelta una resina di Ineos Styrolution: l’ASA Luran S.
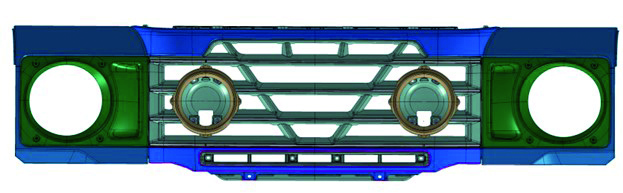
CON IL COMPOSITO VAI DI LUSSO
Il profilo interno del portellone posteriore della berlina DS4 di Stellantis è stato stampato a iniezione da Flex-N-Gate con il polipropilene rinforzato con fibre di vetro corte Thermofil HP: grazie alla distribuzione uniforme delle cariche, il materiale è congeniale alla realizzazione di questo componente di notevoli dimensioni, che accoglie inserti metallici ed elementi di fissaggio.
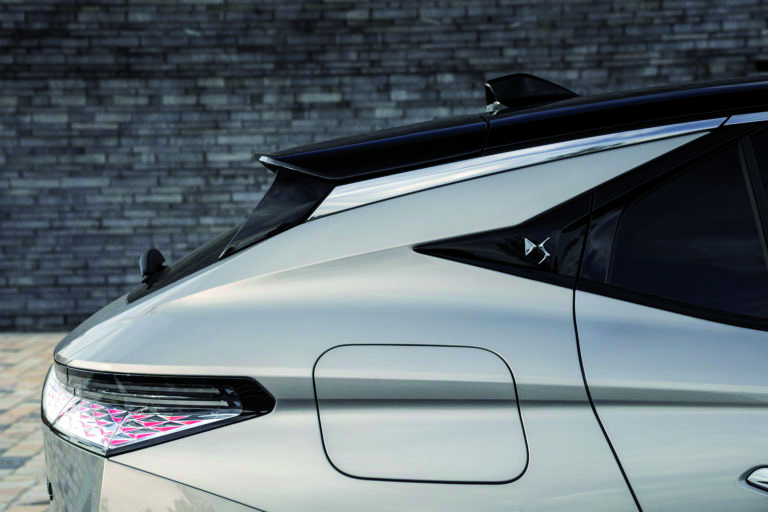
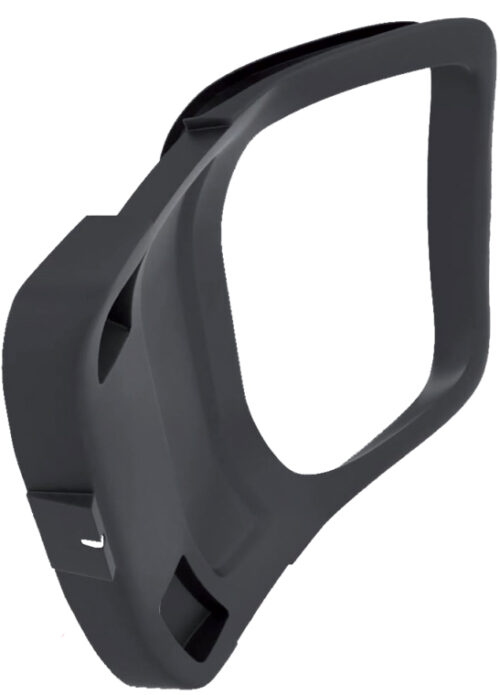
La fluidità della matrice PP di Sumitomo Chemical è rinforzata con fibre corte nel composito Thermofil HP di Sumika Polymer Compound, fornendo prestazioni meccaniche comparabili a quelli dei materiali con fibre lunghe e una finitura superficiale di Classe A, priva di linee di flusso visibili; stampabile con tempo ciclo inferiore del 5% rispetto ai compound concorrenti, il materiale è completamente riciclabile a fine vita.
Leggera, rigida, sicura, una portiera posteriore prodotta con fibra di carbonio presenta molti vantaggi rispetto a quelle metalliche. I tecnici di Hongqi, brand di lusso di FAW Group, sono riusciti nell’impresa di superare i due maggiori ostacoli al progetto – la scarsa produttività delle tecnologie più diffuse e la difficoltà di un pezzo di grandi dimensioni con geometrie articolate – combinando lo stampaggio di compositi termoplastici con l’iniezione di inserti funzionali. Il sistema di riscaldamento integrato nello stampo conferisce alla parte la resa estetica richiesta; la fibbia di chiusura della cintura di sicurezza, stampata a iniezione, è solidamente unita alla portiera. Le portiere posteriori in composito con fibra di carbonio pesano il 40% in meno rispetto alle versioni in acciaio e la rigidità delle parti fisse è stata incrementata del 10%.
ALZARE L’ASTICELLA SUL… GREEN
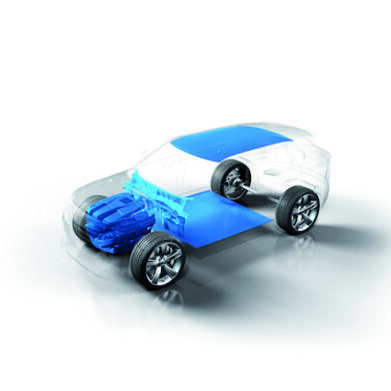
Le prestazioni sono già al massimo, eppure possono essere migliorate: non è un paradosso, per l’industria il nuovo margine di miglioramento è rappresentato dall’impronta al carbonio. La tecnologia del poliuretano espanso viscoelastico Acustiflex VEF Bio di Huntsman conserva l’alto profilo di smorzamento acustico alle basse frequenze (inferiori a 500Hz) a fronte di un contenuto biobased, ricavato da oli vegetali, fino al 20% della formulazione. “Finora l’introduzione di materiali rinnovabili è stata scoraggiata dall’impatto negativo sulle prestazione del materiale, soprattutto in termini di emissioni e odori, ma i nostri sviluppi di espansi poliuretanici privi di ammine e plastificanti e a ridotto rilascio di aldeidi hanno smentito questa difficoltà”, spiega Irina Bolshakova, responsabile marketing per i poliuretani dedicati al settore auto di Huntsman. Il nuovo sistema permette di diminuire le emissioni di anidride carbonica fino al 25% nei supporti per tappetini auto ed è applicabile anche ad elementi isolanti per cruscotto e passaruota. Il contenuto biobased non appesantisce la formulazione, adatta per parti con geometrie complesse e spigoli vivi con un tempo di distacco dallo stampo fino a 80 secondi.
L’arco della maniglie delle vetture Mercedes-Benz Classe S ed EQE è stampato a iniezione con la poliammide 6 Ultramid di Basf, caricata al 30% con fibra di vetro. La resina è stata ottenuta dall’olio di pirolisi che Pyrum Innovations ha ricavato da scarti di pneumatici e da biometano derivato da rifiuti dell’industria agroalimentare: seguendo lo schema REDcert2, le quantità richieste per sostituire le materie prime fossili nel prodotto finito sono certificate, le resine sono inserite nel network produttivo di Basf tramite il calcolo del bilancio di massa e trasformate da Witte Automotive.
La soluzione sarà applicata anche all’assorbitore d’urto frontale montato sui modelli Classe S.
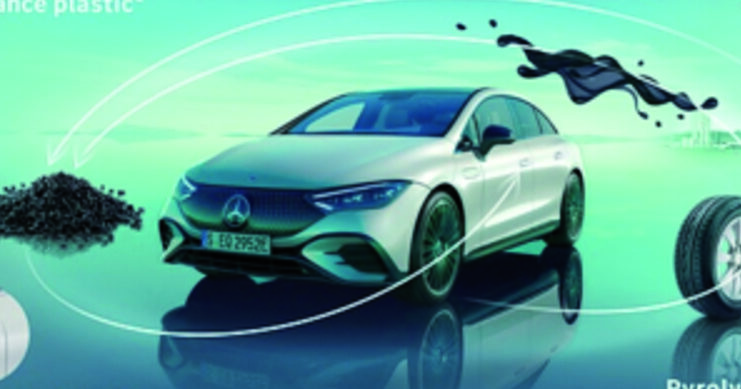
A.F.